Rutgers CAIT recently enhanced capability in large-scale structural-testing equipment that will enable full utilization of its existing laboratory infrastructure and expand its portfolio in transportation research by providing access to a capability that currently does not exist in any other university in New Jersey and the local region. The expansion is facilitated by an ongoing UTC project developing a cost-effective standard open rib steel orthotropic bridge deck that provides an innovative deck solution with improved durability and extended service life necessary for economically maintaining national bridge infrastructure in a state of good repair.
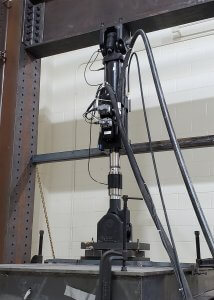
Bridge deck testing with the new equipment at the Rutgers CAIT laboratory. Photo ©Dr. Sougata Roy.
Among all components in the highway bridge infrastructure, bridge decks experience the most deterioration resulting from exposure to vehicles on the roadways, severe weather, and winter deicing agents.
Finding a way to extend the life and state of good repair of bridge decks across the country, and particularly in the complex Northeast region, is a key durability challenge facing transportation today. A Rutgers Center for Advanced Infrastructure and Transportation (CAIT) University Transportation Center (UTC) research project is addressing this emerging need by developing a family of cost-effective steel orthotropic bridge decks (SOBD) with open ribs.
Dr. Sougata Roy, an Associate Research Professor at Rutgers and a CAIT-affiliated researcher, is leading this research effort as the Principal Investigator.
“Due to lower initial cost, traditional reinforced concrete is the most common choice for bridge decks,” Dr. Roy said. “However, these decks are inherently susceptible to corrosion damage requiring repeated repair and replacement, diminishing useful service life of bridge infrastructure and increasing life-cycle costs. An alternative, cost-effective deck solution demonstrating improved durability and extended service life is necessary for economically maintaining the national bridge infrastructure in a state of good repair.”
“Laboratory testing and service performance have demonstrated the potential for SOBDs—which are a stiffened steel plate deck integral with the primary floor framing of the bridge structure—when it comes to providing a durable and life-cycle cost-effective solution,” said Dr. Roy, an expert in fatigue and fracture of highway infrastructure. “Made from a sustainable material, SOBDs have the benefits of being lightweight and structurally efficient, resilient, and able to facilitate accelerated construction.”
Despite these benefits, however, the use of SOBDs in the U.S. has been mostly limited to long span signature bridges and movable bridges. Use on routine short and medium span bridges, which constitute the majority of the highway bridge inventory, has been held back due to a lack of robust standards and relatively high initial cost of fabrication, he said. The aim is to innovate easy-to-fabricate connections that will facilitate domestic fabrication leading to standard “off-the-shelf” deck designs and widespread use.
With this mission, Dr. Roy is also co-leading a FHWA funded Small Business Innovation Research (SBIR) effort with ACROW Bridges of Parsippany, New Jersey, innovating a steel sandwich panel bridge deck that will speed up bridge construction many folds, maintaining the same standards of durability and service life.
“Developing cost-effective bridge decks for improved durability and extended service life requires laboratory experimentation and fatigue testing of bridge decks to simulated highway loading,” Dr. Roy said. “Not only for vehicular loading, fatigue testing of connections in highway structures simulating wind load effects are also necessary for improving the inventory. To perform these tests, and other cutting-edge research that addresses emerging needs in transportation—modern, large scale structural testing capability was needed.”
Answering this need, Rutgers CAIT procured state-of-the-art hydraulic testing equipment that can deliver 30 gallons of flow per minute to a suite of servo hydraulic actuators that can apply up to a 110,000-pound force and 10 inches of movement.
The equipment incorporates extreme flexibility that can impose monotonic, reverse cyclic, and fatigue loading in configurations as needed, and will be sufficient to conduct a wide range of structural testing for varied applications, Dr. Roy said.
“This equipment will enable full utilization of the existing laboratory infrastructure and will expand Rutgers University’s portfolio in transportation infrastructure research by adding new large scale structural testing capabilities,” said CAIT Director Dr. Ali Maher. “Currently, this capability is unique to CAIT and Rutgers with no parallel in any other institution in the region.”
The improved capabilities are also expected to help facilitate cross-cutting structural engineering research and collaboration among universities in the region such as UTC partners at Princeton, NJIT, Rowan, and others, Dr. Maher said, while also producing new educational opportunities for students.
“By expanding our capabilities with this new technology, we can now look at developing innovative off-the-shelf bridge deck solutions that can be economically fabricated,” said Dr. Roy. “This will be a game changer in productivity and competitiveness of American steel bridge fabrication industry, and will revolutionize the design, construction and maintenance of routine short and medium span highway structures that make up the majority of the highway bridges in this country. The opportunities are endless.”