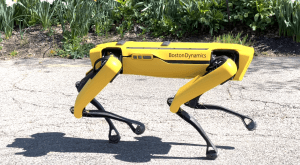
Spot can be operated autonomously with a tablet controller, allowing for the safe inspection of hard-to-reach infrastructure assets.
Able to climb stairs, navigate rough terrain, and respond to commands, the mobile robotic dog, “Spot,” offers Rutgers CAIT researchers an autonomous technology for innovations in infrastructure maintenance and repair.
Robots are an emerging force in the infrastructure repair and maintenance industry. From flying drones to smart and autonomous robotic systems, these innovations are poised to make a dynamic contribution to infrastructure repair and maintenance activities.
One of these new technologies is Spot, a mobile robotic dog platform from Boston Dynamics that can navigate rough terrain and allow researchers to enhance and automate infrastructure inspection projects in a way that is efficient, safe, and accurate.
Operated with a tablet controller, users can set Spot’s body positioning, obstacle avoidance, navigation routes, and more with the touch of a few buttons, according to Boston Dynamics. Once set up, the adaptive system can be deployed and inspect hard-to-reach or dangerous environments, carry infrared cameras and other imaging devices on unstable terrain, automate data collection, and more depending on user needs.
Jie Gong, an associate professor at the Rutgers University School of Engineering acquired the robotic platform as part of a Center for Advanced Infrastructure and Transportation (CAIT) University Transportation Center (UTC) research grant supporting maintenance and robotic systems. The purchase was a collaborative effort between the Rutgers University School of Engineering and its Strategic Equipment funds, the Department of Civil and Environmental Engineering, and Rutgers CAIT.
His project, “Delivering Maintenance and Repair Actions via Automated/Robotic Systems,” will identify gaps in infrastructure asset management and highlight opportunities for developing and deploying autonomous systems that can streamline and enhance the quality of common repair and maintenance projects with the overall goal of enhancing the durability of transportation infrastructure.
“Boston Dynamics’s Spot platform will enable us to deploy inspection sensors such as infrared cameras and 3D imaging devices on dynamic infrastructure construction sites in ways that were too dangerous or not possible before,” Gong says. “Because the robot can climb stairs, navigate rough terrain, and walk on sloped surfaces autonomously while mapping its environment, inspecting highways, bridges, transit stations, and other vital infrastructure can be done in a faster, safer, and more accurate way.”
He explains that intelligent, robotic systems can transform an inspector’s job by solving inherent challenges in the field—such as mishaps that occur due to tedious or dangerous conditions—creating a future where robots are common tools inspectors can use to automate aspects of the job. This technology can help alleviate dangerous work environments, get a more accurate and holistic view of different infrastructure assets and environments, and be an innovative tool for maintaining the vast transportation network and aging infrastructure in the United States while supplementing the construction workforce.
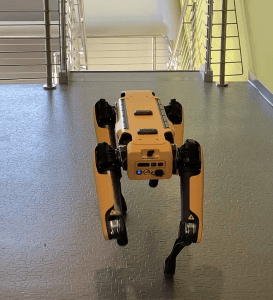
The mobile robotic dog Spot from Boston Dynamics can navigate different terrain, climb stairs, and more with the touch of a few buttons.
“Still to this day infrastructure repair and maintenance projects heavily rely on construction crews equipped with machinery tools,” Gong says. “Often these traditional methods call for the shutdown of roads and bridges that can be costly and disrupt traffic, put workers in live traffic conditions that can be dangerous, and require the inspection of places that are hard to reach by people.”
Some of Gong’s other recent research has included using remote sensing to gather geospatial big data and apply data analytics to understand building and infrastructure performances during natural disasters. He has led post-disaster reconnaissance missions following Hurricane Sandy and other natural disasters with the goal of advancing damage assessment methods and turning disaster data into actionable knowledge for resilient rebuilding.
He anticipates that Spot’s ability to inspect and navigate similar dangerous environments while carrying critical equipment and automating data collection will make it a valuable asset going forward.
CAIT director and professor of civil and environmental engineering Ali Maher believes the new technology also has the potential to help facilitate collaboration between UTC partner schools and address the various additional asset management and maintenance needs of CAIT’s regional transportation stakeholders in future research projects.
“This robotic platform brings new capabilities to CAIT in terms of rapid and efficient condition assessment and inspection for general infrastructure asset management and more specifically deciding on when and what to repair and maintain,” Maher says. “We look forward to using this technology in helping our stakeholders address critical transportation needs in the region moving forward.”