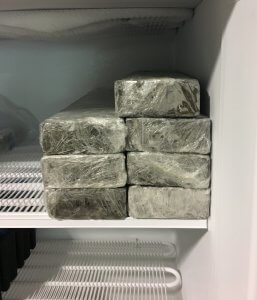
Frozen concrete prisms waiting to be tested. Photo ©Matthew P. Adams.
By subjecting samples of “repaired” concrete to 300 cycles of freezing and thawing, UTC partners at NJIT can simulate the freeze-thaw damage that concrete will see over a lifetime. With this information and additional testing, they are developing a guideline on freeze-thaw damage and rapid-repair materials that will give agencies the tools to select the right materials, save money on repair costs, and improve system resiliency overall.
Damage to concrete roadways occurs because of poor construction quality, accidents, severe environmental conditions, and general wear and tear. Using rapid-repair materials allows transportation agencies to repair the infrastructure without causing undue service delays and without having to completely shut down roadways, bridges, or tunnels.
Unfortunately, improper use of rapid-repair materials can lead to accelerated deterioration, or the need to re-repair within a short time period. This becomes time consuming and expensive, and happens often for a number of reasons: one being exposure to freeze-thaw cycles.
In New Jersey alone, it has been estimated that road-construction costs total $238,000 per mile, according to the Garden State Initiative, a non-profit research and educational organization.
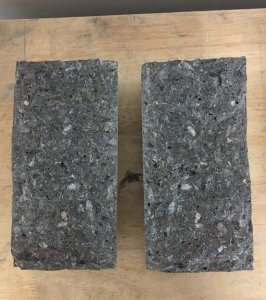
Pictured is a concrete cylinder after being tested for tensile strength. Photo ©Matthew P. Adams.
“A lot of highway construction expenses come from re-repairing earlier repairs,” said Matthew P. Adams, an assistant professor in the Department of Civil and Environmental Engineering at The New Jersey Institute of Technology (NJIT).
Adams, along with Matthew Bandelt, Co-PI on the project and an assistant professor in the Department of Civil and Environmental Engineering at NJIT; Noah Thibodeaux, a graduate research assistant; and researchers at NJIT’s Materials and Structures Lab (MatSlab), is examining freeze-thaw cycles to develop a guideline on how this type of damage impacts the bond and quality of overlays on repairs done with rapid-repair cements.
“When you place a repair on a concrete roadway or bridge deck, there is a seam between the existing substructure and the new material,” Adams said. “This means that moisture can easily get in that space and as water freezes the moisture becomes ice, expands, and causes tensile stress—damaging the concrete.”
This issue affects roads in temperate areas especially, as they will experience both cold winters and hot summer temperatures throughout the year. The New York and New Jersey area sees a significant number of freeze-thaw events in comparison to a lot of other regions of the country, for example.
The short-term goal of the research is to develop a guideline that agencies can implement into their own decision-making processes when evaluating rapid-repair materials, and add to the body of knowledge on this subject, he said. Down the road, researchers hope to develop new methods of testing rapid-repair materials and freeze-thaw cycles so that it becomes standardized.
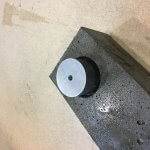
Concrete overlay with cored section prepared for pull-off testing. Photo ©Matthew P. Adams.
“We often hear that different transportation agencies spend a lot of their money on repair of their infrastructure,” Adams said. “So, we’re talking about the durability of rapid-repair materials, specifically the type of materials that a bridge owner or transportation agency may want to use to very quickly close a roadway, make a patch on a bridge deck, and get in and out within a few hours.”
To start, researchers first had to identify the best types of rapid-repair materials in freeze-thaw environments. Adams said that they are studying cement materials based off of calcium aluminate cement, calcium sulfoaluminate cement, and accelerated portland cement. These systems all harden and gain strength rapidly, but they have unique chemical properties that cause them to behave differently.
Two main test methods are being done to examine the durability of these systems: freeze-thaw deterioration with dynamic modulus, and overlay pull-off testing.
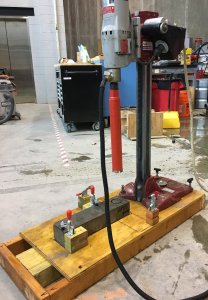
Partial coring of concrete prism to prepare for pull-off testing. Photo ©Matthew P. Adams.
Samples of ordinary concrete are being cast and then “repaired” by roughening the surface and overlaying a section of the rapid-repair material on top, Adams said. These repaired sections are subjected to 300 cycles of freezing and thawing, which simulates damage the concrete will see over a lifetime. Concrete quality is monitored by measuring the dynamic modulus–the time it takes for a soundwave to propagate through a concrete sample–the longer the time, the more damage incurred.
The overlays are also being analyzed through pull-off testing, where a section of the overlay is subjected to a tensile load to check the strength of the bond between the repair and the existing substrate. The pull-off testing is done regularly throughout the freeze-thaw cycling to determine how the freezing and thawing is impacting the bond of the materials.
Results from the study will show what rapid-repair materials and surface preparation techniques are ideal for freeze-thaw situations, Adams said. Additionally, information on the deterioration rate of the bond-zone and overlay material will be gathered. The impact of the research will be measured by comparing the expected lifespan of repair systems using the newly developed approach to traditional systems.
From there, transportation agencies will be able to use these test methods in their own decision-making processes when they have a road in need of treatment.
“Using rapid-repair materials can be the difference between closing a lane for a couple of days and closing it for a couple of hours,” Adams said. “By having the tools to make longer lasting and more durable repairs, agencies will be able to lower the community impacts, costs, and efficiency of having to do them.”