
Chart showing corrosion growth for six different coatings. The six tested were selected based on a 20-year field study in which two of the coatings were weak while two others performed very well. The chosen accelerated test protocol provides a rapid corrosion growth rate resulting in considerable decrease in adhesion strength.
Research by Rutgers and NJDOT Research Bureau is selected in AASHTO high-value research competition
A project by Rutgers distinguished professor and principal investigator Dr. Perumalsamy N. Balaguru, co-PI Dr. Husam Najm, and NJDOT Bureau of Research project manager Dr. Giri Venkiteela was recently announced as a winner in the 2019 AASHTO Sweet 16 Competition. The high-value research project that won them the honor identified a protocol for accepting new overcoating for steel surfaces.
“Overcoating” is a common term for bridge maintenance painting operations that only partially remove existing paint and apply a new coating over the existing paint, bare steel, and rusted surfaces. This practice encompasses—and is very similar to—traditional maintenance and touch-up painting employed for many years. But, overcoating differs from traditional maintenance painting in several ways.
Traditionally, maintenance painting was either done as part of routine life-cycle maintenance (for larger bridges) or in conjunction with other maintenance activities (e.g., steel component replacement). Overcoating is now viewed as an alternative to fully removing and replacing existing paint that is no longer offering adequate protection.
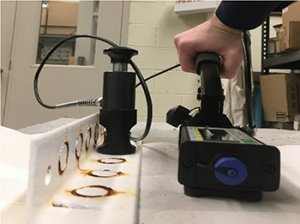
The proposed method is based on direct adhesion strength at various stages of corrosion. The “pull-off” strengths provide quantitative and repeatable measurements for quantifying degradation of the substrate. Details on testing methodology and results are available in the final report.
Due to ever-tighter budgets, some bridge owners even use it as a primary bridge rehabilitation option and a reasonable substitute for abrasive blasting and complete repainting. In the past, maintenance painting has generally used coatings similar to the existing coating, for example, using a lead-containing alkyd over an existing lead-containing alkyd. Now, overcoating may involve materials that are vastly different from the original coating.
With these options, a new protocol to evaluate corrosion-inhibiting efficacy and durability of coating options that would to streamline decision making was needed. But how can DOTs zero-in on the right new coating without prolonged field testing or even accelerated lab testing?
Major differences between the current method and the method proposed in the research are striking. For example, current testing takes two years to complete. Balaguru’s method reduces the timeframe to six months. The test chamber also is very economical to build, costing around $30,000 instead of quotes received as high as $250,000. And, instead of monitoring two samples and taking measurements, the new method measures strength at three different locations at least nine times, which provides good statistical quality assurance.
Additionally the method proposed in this research measures corrosion creep from a coating-damaged location after exposure to accelerated corrosive conditions that include deep freezing. It is based on direct adhesion strength at various stages of corrosion; the “pull-off” strengths provide quantitative and repeatable measurements for quantifying degradation of the substrate.
Details on testing methodology and results are available in the final report.
Sweet 16 award-winners are recognized and invited to give a presentation during the Sweet 16 session at the 2019 AASHTO Research Advisory Committee (RAC)/TRB Representative Annual Meeting in July as well as a poster session at the TRB Annual Meeting. RAC also publishes an annual compilation of all these projects, Research Impacts: Better–Faster–Cheaper. This document is a great resource to DOTs and helps eliminate or reduce duplication of research.
A history of high-value research from CAIT
Two CAIT projects conducted with the NJDOT Bureau of Research were published in the 2018 Research Impacts: Better–Faster–Cheaper compilation.
“Evaluation of Raised Pavement Markers” was a nearly $300,000 project led by PI Dr. Xiang Liu.
Raised pavement markers (RPMs) have been used throughout the world since the 1930s. In the New Jersey, RPMs are used along all centerlines and skip lines, regardless of traffic volume, roadway geometry, or roadway classification. The extensive use of RPMs has increased interest in understanding the safety benefits of RPMs, promising cost-effective alternatives or modifications, and best practices in maximizing their utility. The project entailed a comprehensive literature review on this subject resulting in two main observations:
1. There is no consensus regarding whether and how RPMs affect crash rate. Depending on scope and data, different studies report different magnitudes of safety changes (positive or negative) after RPMs are implemented.
2. There are various alternatives and modifications possible for RPMs, such as rumble strips and traffic tape. The use of these alternatives varies by state.
A future phase of the project will develop a methodological framework for quantifying the cost-effectiveness of RPMs and their alternatives based on specified road and traffic characteristics.
“The Use of Porous Concrete for Sidewalks” evaluated various factors that influence the performance of porous concrete sidewalks. These include hydraulic performance to meet Department of Environmental Protection (DEP) regulations, structural performance to meet typical sidewalk strength requirements, and life-cycle cost and maintenance requirements. Co-PIs on the project were Dr. Hao Wang, Dr. Husam Najm, and engineering researcher John Hencken.
Several mix designs were tested to evaluate structural and hydrological performance and energy budget. A cost-benefit analysis comparing porous pavements for sidewalks to conventional concrete and asphalt alternatives, including environmental permitting, initial construction, and maintenance costs was performed.
The study found the use of porous concrete for sidewalks can be effective in mitigating stormwater runoff. For soils with low permeability, an auxiliary subsurface drainage system may be needed. A porous sidewalk needs to be periodically maintained to avoid clogging resulting from debris and sediments. Porous sidewalks should be free from water especially in the winter to avoid failure due to freeze and thaw. Resistance to raveling is very important for the long term performance of pervious concrete. There is a need for research to evaluate raveling resistance and factors than can influence this resistance such as aggregate type, addition of sand, cement content and chemical additives.
June 2019